
TOOLING
Moulds and prototypes

Tooling
Three Questions...
-
How many parts do you plan to make and at what output rate?
-
What production process and materials are you considering?
-
Will this prorotype require some design iterations?
Triac Composites' Design team can support you
Depending on the answers to the above questions and the design detail, we will quote and make appropriate recommendations.
For example, carbon moulds are used with carbon parts in the autoclave where dimensional stability of mould and part materials match when heating.
Solid blocks are used for complex part geometries with fine tolerances where we can use our CNC Machine (Computer Numerical Control Machining is a process used in the manufacturing sector that involves the use of computers to control machine tools) to cut 100 per cent of the mould surface.
Step 1 - Plug Assembly
-
UPDATE 11 April 2019: Triac Composites has purchased a robot for carving out the plugs. For further information, click here.
-
CNC cut sections with alignment marks and assemble like lego.
-
Skin with planks or sheet depending on geometry.
-
Seal with fibreglass shell and tune surface shape using a fairing compound.
Step 2 - Mirror Polish
Using high build primers and hardened topcoat paints, sand. And then sand. And then sand some more...
The finish here directly affects the final part surface. A release agent must be added to ensure it doesn't stick when making the mould.
Step 3 - Mould lamination
-
The tooling gelcoats used in the moulds must be low-shrink, hardened and a contrasting colour to your final part.
-
Build up the shell thickness by hand lamination using low-shrink tooling resin. Be careful, particularly in the first layers, to avoid air bubbles. To prevent deformation of the prized surface, don't let it get too hot.
-
Add reinforcements, wheels and lifting points.
The moment of truth
Demoulding and turning over the mould is quite an experience... Will it "come out nice"??? Are the
lifting points strong enough? Did we calculate the
centre of balance for rotation correctly?
Fortunately, at Triac Composites, we have done
this hundreds of times so, invariably and inevitably,
it all goes smoothly.
After a quick clean, seal and release, the mould is
ready to produce hundreds of parts.
Destruction mode
Now that we have a beautiful, new mould, the
plug has outlived its usefulness! That's right, it's now
scrap - as per the side photo.
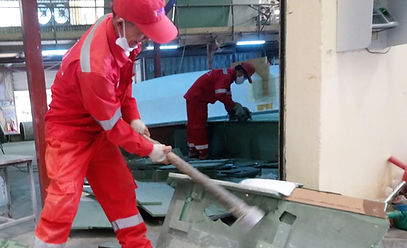